Снижение расхода смазки в поршневых компрессорах
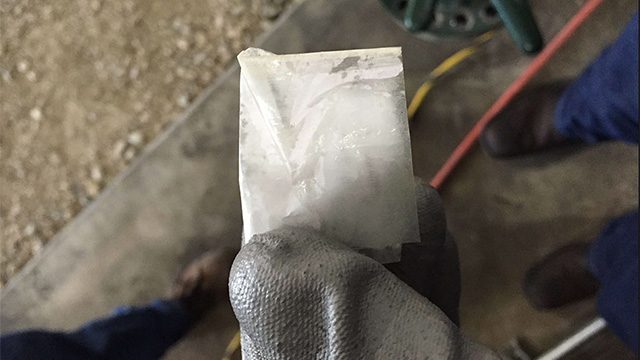
Авторы: Джастин Йенц и Джо Хаган — Ariel Corporation, Маунт-Вернон, Огайо, США
Аннотация
Десятки тысяч поршневых компрессоров, работающих в Северной Америке, ежегодно потребляют смазочного масла на сумму в 250 000 долларов США. Как правило, большинство этих компрессоров потребляют больше масла, чем необходимо, поэтому эксплуатационные расходы можно значительно снизить. Сокращение затрат может быть достигнуто путем относительно простых шагов по определению правильного типа и количества масла, поставляемого к каждой точке подачи смазки, без изменения конструкции или материалов изнашиваемых компонентов. В этой статье описывается установленный метод, а также шаги по обеспечению правильной работы системы смазки с целью обеспечить долгосрочную и надежную работу компрессора.
Введение
Обеспечение правильной смазки поршневых газовых компрессоров является обязательным условием надежной работы оборудования. Компрессоры чаще всего работают непрерывно, что приводит к значительному увеличению времени работы изнашиваемых компонентов. В поршневых компрессорах используются две система смазки, которые подают масло к критически важным компонентам в приводной передаче, цилиндрах и сальниках. Первая — это рециркуляционная система, которая защищает подшипники, втулки, упорные пластины и крейцкопфы в приводной передаче. Вторая система — это система «одноразовой смазки», которая подает масло в зеркало цилиндра, на поршневые кольца, в поршневой шток и на кольца сальника. Основное различие между этими двумя системами состоит в способе использования масла. Приводная передача многократно использует масло перед тем, как его необходимо будет заменить. В системе смазки цилиндра масло используется только один раз, после чего оно расходуется в процессе сжатия. Эффективное использование масла в системе смазки цилиндров является ключевым моментом для минимизации эксплуатационных расходов при максимизации надежности работы оборудования. В этой статье представлен установленный метод обслуживания системы смазки цилиндров и определения надлежащего расхода смазки.
В системе смазки цилиндров, также называемой «лубрикаторной» системой, используется объемный поршневой насос для подачи масла к распределительному клапану, который дозирует масло по критически важным областям внутри цилиндра и сальника. Расход масла в критических областях составляет порядка капель масла в минуту. Масло должно подаваться под давлением, достаточным для преодоления давления газа в каждой критической области. Значения давления обычно меняются от почти атмосферного до 3000 фунтов на кв. дюйм. Как только масло закачивается в критическую область, оно либо перемещается в область более низкого давления, либо смешивается с газом, проходящим через компрессорный цилиндр. Компрессор мощностью 1000 л. с. может потреблять 2000 галлонов масла в год, а более крупные компрессоры — до 6000 галлонов в год. Учитывая, что цена на минеральное масло может колебаться от 7 до 15 долл. США за галлон, а на синтетические смазочные материалы — от 20 до 50 долл. США за галлон, ежегодная стоимость масла для одного компрессора может достигать 250 000 долл. США. В эту ежегодную стоимость не входят сопутствующие затраты на сбор, транспортировку и утилизацию масла, покидающего компрессор. Эти дополнительные затраты могут значительно увеличить ежегодные расходы на масло, связанные со сжатием.
Проектные соображения
Газовые поршневые компрессоры применяются в самых разных сферах. Производитель компрессора должен оценить подробности каждого случая применения с целью определения наихудшего варианта эксплуатации, чтобы можно было рекомендовать тип масла и расход смазки. Обычно «наихудшим» вариантом является эксплуатация с наибольшим давлением нагнетания на конечной ступени. Рекомендуемый тип масла выбирается на основе ожидаемой потери вязкости после того, как масло закачано в каждую критическую область системы смазки цилиндра. На вязкость масла влияет состав газа, чистота, давление и рабочая температура. Как правило, более тяжелые газообразные углеводороды и более высокое давление нагнетания приводят к тому, что цилиндровое масло становится менее концентрированным, что вызывает снижение вязкости и истончение масляных пленок, защищающих компоненты. Чтобы избежать слишком большой потери вязкости, рекомендуется использовать более тяжелые минеральные масла или синтетические смазочные материалы класса ISO, устойчивые к расжижению.
Жидкие загрязняющие вещества (такие как вода и углеводороды) и недостаточность смазки также влияют на качество масляной пленки, снижая вязкость масла и/или разрушая масляную пленку. Плохое смазывание приводит к повышению температур, что уменьшает срок службы компонентов. В худшем случае неконтролируемый нагрев может привести к быстрому выходу компонента из строя.
Значения расход смазки определяют, как часто нужно добавлять масло в критические области системы смазки цилиндров. Производители оригинальных компрессоров разработали собственные способы определения расхода смазки. Ariel начинает с «базового расхода», который колеблется от 0,3 до 0,5 пинты в день на дюйм диаметра детали (пример расчета см. в приложении А). Базовый расход определяется размером станины компрессора. Расход смазки регулируется при помощи «Множителя базового расхода» в зависимости от давления нагнетания и состава газа. Множитель базового расхода изменяется в диапазоне от 0,5 до 3 в зависимости от сложности условий эксплуатации. Расчет определяет «нормальный» расход смазки для компонента, работающего при номинальной частоте вращения станины. Работа на более низких скоростях пропорционально снижает расход (при работе на сниженной вдвое скорости требуется половина «нормального» расхода смазки при номинальной частоте вращения). В течение первых 200 часов работы компрессора рекомендуется использовать расход смазки в режиме «приработки», в котором количество масла увеличено на 150–200% относительно «нормального» расхода. Дополнительное масло для приработки помогает охладить компоненты и смыть продукты износа по мере приработки компонентов.
Рекомендованные коэффициенты цилиндра и типы масла в большинстве случаев являются консервативными, чтобы учесть некоторый уровень неизвестных или нештатных условий. Рекомендации по смазке составлены на основе группировки сфер применения по общим категориям газовых потоков. Две сферы применения могут относиться к одной категории, но отличаться по агрессивности условий по отношению к смазочному маслу. В зависимости от интенсивности эксплуатации обычно можно ожидать некоторого снижения расхода смазки после окончания периода приработки. Если система смазки цилиндра в компрессоре была рассчитана на «приблизительный» набор условий, это может привести к тому, что тип масла или значение расхода смазки окажутся совершенно не подходящими для реальных условий или будут избыточны для них. В некоторых случаях это может повлиять на выбор распределительного клапана, на подбор характеристик насоса принудительной подачи и на необходимость использовать независимый подвод масла, если рекомендации по маслу не подойдут и для станины компрессора.
Важно отметить, что сальники могут вырабатывать различное количество тепла в зависимости от сферы применения компрессора. Дополнительное тепло, выделяемое сальником, может потребовать увеличения рекомендуемой вязкости масла для компенсации потери вязкости при повышенной температуре. Выделение большого количества тепла потребует охлаждения сальника водой или в некоторых случаях маслом для поддержания приемлемой рабочей температуры.
Соображения относительно снижения расхода смазки
На требования к расходу смазки, а также на надежность подачи масла к критическим участкам в системе смазки цилиндра могут влиять многие факторы. Ниже приведены наиболее распространенные факторы, которые необходимо учитывать перед изменением значения расхода смазки.
Факторы, влияющие на расход смазки
- Состав и качество газа
- Рабочая скорость компрессора
- Тип масла и класс вязкости для системы смазки цилиндра
- Геометрия детали (например: размер зеркала цилиндра)
- Давление нагнетания цилиндра
- Рабочая температура
- Подбор характеристик насоса принудительной подачи и распределительного клапана
- Рециркулирующий газ, насыщенный смазочным маслом
- Отключение цилиндра
- Частые запуски/остановки
Факторы, влияющие на подачу масла
- Износ насоса принудительной подачи и отверстия/поршня распределительного клапана
- Установка и подбор характеристик балансировочных клапанов
- Правильное расположение линий подвода/отвода смазки распределительных клапанов
- Утечки: поврежденные соединения, трубки, фитинги, уплотнительные кольца
- Износ и изменения в геометрии смазываемых компонентов
- Расположение линии подачи масла (от бака суточного запаса)
- Подбор характеристик линии для улучшения потока масла
- Утепление трубопровода для улучшения потока масла
- Фильтрация для улучшения качества масла
- Неисправный обратный клапан
Перед тем, как приступить к снижению расхода смазки, необходимо проверить текущую конфигурацию компрессора. При этом можно обнаружить факторы, которые возникли в ходе эксплуатации или не были учтены при исходном расчете параметров системы смазки цилиндра. Перед снижением расхода смазки необходимо правильно настроить систему смазки цилиндра и убедиться в ее работоспособности (надежности). Системы должны характеризоваться удовлетворительным сроком службы компонентов и высокими рабочими характеристиками до снижения расхода смазки.
Система смазки цилиндров обычно рассчитана на конкретные «наихудшие» условия эксплуатации или ситуации применения компрессора. Система должна выдерживать самые тяжелые условия эксплуатации компрессора. В зависимости от возраста оборудования или подобранных характеристик установки система смазки цилиндров может больше не работать должным образом или не соответствовать условиям эксплуатации компрессора. Возможно, придется обновить оборудование системы смазки цилиндра, а также карты смазки, чтобы добиться надлежащего исходного расхода смазки для текущих условий эксплуатации.
Уменьшение расхода смазки должно производиться методично, чтобы избежать условий недостаточной смазки, которые могут привести к случайному повреждению компонентов из-за повышения рабочих температур. Избыточные температуры могут привести к выходу из строя поршневых колец или колец сальников, а также других основных компонентов, таких как поршневые штоки и зеркала цилиндров. Выход компонентов из строя может повлечь за собой значительные расходы в зависимости от их серьезности:
- трудозатраты (сверхурочные) = 2000 долл. США в сутки;
- замена сальников и поршневых колец = 3000 долл. США;
- срочная доставка = 4000 долл. США;
- замена цилиндра = 25 000 долл. США;
- потеря продукции = 40 000 долл. США в сутки.
Процесс снижения расхода смазки необходимо выполнять постепенно и проводить периодические проверки после каждого снижения. Это поможет проверить объем масла и качество работы компонентов. Признаки достижения нижнего предела смазки для нормальной работы укажут на необходимость увеличения расхода смазки. Осмотр масляных пленок внутри сальника затруднен из-за конструкции картера. Чтобы фиксировать изменения рабочих условий таких компонентов, можно отслеживать утечку в дренажной линии и/или контактную температуру трубок. Необходимо обеспечить постоянства точки проверки трубок (как можно ближе к корпусу сальника) и способа проверки контактной температуры.
Расход смазки во время приработки
В новые кольцевые компоненты добавляется дополнительное масло по мере их приработки в течение первых 200 часов работы. По завершении периода приработки расход смазки необходимо вручную снизить с расхода в режиме «приработки» до «нормального» расхода. Переход к нормальному уровню расхода смазки обычно снижает расход масла на 33–50%. Если в результате недосмотра расход смазки не был снижен после периода приработки, некоторое оборудование может в течение длительного времени работать с расходом режима приработки.
Проверка перед снижением расхода смазки
Важно выявить любые случаи ускоренного износа таких компонентов, как поршневые кольца, опорные кольца и сальники, которые возникали в прошлом. Проблемы, связанные с изнашиваемыми компонентами, могут привести к необходимости проведения дальнейшего анализа характера отказа и могут стать причиной приостановки любого процесса снижения расхода смазки до тех пор, пока не будет проведен дальнейший анализ.
Чтобы упростить распознавание любого ускоренного износа компонентов, смазываемых лубрикаторной системой смазки, необходимо провести тщательную проверку. Необходимо зафиксировать следующие параметры.
- Замеренный объем утечек и температура дренажа сальников перед остановом
- Диаметр поршневого штока
- Ширина и глубина канавок поршневых/опорных колец
- Внутренний диаметр зеркала цилиндра
- Глубина секций/чашек и общая длина корпуса сальника
- Радиальная толщина и ширина поршневых колец
- Радиальная толщина и ширина опорных колец
- Тест папиросной бумагой, показывающий качество смазки зеркал цилиндров всех ступеней
- Необходимо удостовериться, что лубрикаторная система смазки работает исправно. В проверку необходимо включить испытание распределительных клапанов на герметичность.
Ниже приведен перечень инструментов, необходимых для первоначальной проверки и дальнейших проверок.
- Расходомер газа для измерения утечки сальника
- Устройство для контроля температуры дренажа/сброса сальника
- Штангенциркуль
- Микрометры измерения наружного диаметра для замера канавок всех поршней
- Микрометры измерения внутреннего диаметра или нутромеры для замера диаметров зеркал цилиндров
- Микрометр измерения глубины
- Невощеная папиросная бумага
Когда вся информация перед проведением испытаний будет собрана, условия применения можно рассмотреть на предмет дальнейшего снижения расхода смазки. Если все проверки покажут, что установка не подверглась чрезмерному износу и все ее изнашиваемые компоненты хорошо смазываются, можно ввести процедуру уменьшения смазки и следовать ей.
Процедура уменьшения объема смазки в полевых условиях
Как только установлено, что условия применения подходят для уменьшения смазки, необходимо ввести процедуры, обеспечивающие правильное нанесение смазки на все компоненты принудительной подачи, а также тщательно контролировать рабочие параметры. Чтобы определить надлежащий объем смазки для всех компонентов, необходимо проводить регулярные проверки. Ниже приведен состав этих проверок.
- Тест смазки цилиндра с использованием бумаги
- Этот тест определяет объем масла, присутствующего на зеркале цилиндра, путем переноса масла с зеркала на тонкие слои невощеной папиросной бумаги.
- Тест бумагой должен быть выполнен в течение одного часа после остановки установки, чтобы получить наилучшее представление о масляной пленке на цилиндре во время работы. Тест проводится следующим образом.
- Слегка протрите зеркало цилиндра двумя слоями обычной невощеной папиросной бумаги. Начните сверху и протирайте по направлению вниз под углом приблизительно 20° (от 1/4 дюйма до 4-5/8 дюйма в зависимости от размера зеркала цилиндра) вдоль окружности зеркала цилиндра. Бумага, соприкасавшаяся с зеркалом цилиндра, должна иметь следы масла (намокнуть от масла), но второй слой бумаги не должен промокнуть насквозь.
- Повторите проверку с обеих сторон зеркала цилиндра примерно на 90° от верхнего края, используя по два слоя чистой бумаги с каждой стороны. Если бумага, соприкасавшаяся с поверхностью зеркала цилиндра, не промокла насквозь, это может указывать на недостаток смазки; если насквозь промокли оба слоя бумаги, это может говорить о ее избытке.
- Утечка сальника
- Скорость утечки сальника является показателем того, насколько хорошо кольца сальника обеспечивают уплотнения, а также указывает на износ или повреждение уплотнительных поверхностей.
- Измерьте утечку сальника из дренажа/сброса сальника, чтобы отслеживать повышенную утечку газа. Это можно сделать с помощью переносного или стационарного прибора учета расхода газа.
- Измерьте температуру дренажа сальника как можно ближе к направляющей крейцкопфа. Измеренное значение укажет на наличие повышенной утечки сальника. Если используется инфракрасный измерительный прибор, обязательно примите во внимание излучательную способность и область вокруг измеряемой поверхности. Измерение базовой температуры с новым сальником необходимо для выявления любого увеличения утечки.
- Осмотр зеркал цилиндров, отсеков направляющих крейцкопфа и поршневых штоков
- Изношенные поверхности скольжения могут ускорить износ колец и увеличить утечку.
- Осмотр зеркал цилиндров и отсеков направляющих крейцкопфа для выявления любых материалов износа, которые были удалены с компонентов.
- Поршневые штоки следует визуально осмотреть на предмет царапин или признаков перегрева.
Проверки должны проводиться с указанной ниже периодичностью.
Таблица 1. Временные интервалы уменьшения объема смазки
Пройденное время | Полная наработка | Полное снижение расхода относительно номинального (%) | |
---|---|---|---|
Выполните пуск с приработочным расходом | 0 | 0 | |
Приработочный расход составляет 150–200% от номинального | |||
Отрегулируйте систему на номинальный расход масла | 200 часов | 200 часов | 0 |
Проверьте условия | |||
Снизьте расход масла на 10% от номинального | 1 месяц | 1 месяц | 10 |
При удовлетворительном результате остановите для проведения проверки, затем перейдите к следующему шагу | |||
Снизьте расход масла еще на 10% | 1 месяц | 2 месяца | 20 |
При удовлетворительном результате остановите для проведения проверки, затем перейдите к следующему шагу | |||
Снизьте расход масла еще на 10% | 1 месяц | 3 месяца | 30 |
При удовлетворительном результате остановите для проведения проверки, затем перейдите к следующему шагу | |||
Снизьте расход масла еще на 10% | 1 месяц | 4 месяца | 40 |
При удовлетворительном результате остановите для проведения проверки, затем перейдите к следующему шагу | |||
Снизьте расход масла еще на 10% | 1 месяц | 5 месяцев | 50 |
При удовлетворительном результате остановите для проведения проверки, затем перейдите к следующему шагу | |||
Снизьте расход масла еще на 10% | ~6 месяцев | 8000 часов | 50 |
Останов для полной проверки |
В дополнение к проверке, описанной выше, по завершении испытаний на отметке в 8000 часов необходимо демонтировать поршневые группы для осмотра канавок поршневых колец, самих поршневых колец, опорных колец, поршневых штоков и зеркал цилиндров. Все размеры следует сравнить с исходными замерами в начале испытаний, чтобы выявить значительный износ.
Если на любом этапе испытаний утечки/температура сальников увеличится или объем смазки любого из цилиндров окажется недостаточным, снижение расхода смазки следует прекратить. Если цилиндры смазываются недостаточно, необходимо увеличивать расход масла с шагом 10% до достижения требуемой масляной пленки на поверхностях цилиндров. Если в конкретную точку подачи смазки поступает едва достаточное количество масла, производитель комплексного оборудования (OEM) компрессора, возможно, сможет изменить конфигурацию распределительных клапанов, чтобы направить масло в данные точки подачи смазки на основе результатов теста бумагой. В идеале все точки подачи смазки цилиндра должны иметь достаточно масла на зеркале цилиндра, чтобы пропитать только один слой папиросной бумаги.
Приложение А.
Пример расчета расхода смазки Ariel
Смазочное масло цилиндра/сальника Ariel
Базовый расход, пинт в сутки на дюйм
(литров в сутки на мм) диаметра на основании класса станины компрессора
JG:A:I:M:N:P:Q:R:S:W 0,3 (0,0056)
JGH:E:J:ACF 0,4 (0,0074)
JGK:T:C:D:F:Z:U:B:V, KBB:V 0,5 (0,0093)
Точки подачи смазки цилиндров
Диаметр зеркала цилиндра X Базовый расход X Множитель базового расхода = Пинт в сутки
Общий расход смазки делится поровну между несколькими точками подачи смазки на одном зеркале цилиндра.
Расход смазки сальника
2 X Диаметр поршневого штока X Базовый расход X Множитель базового расхода = Пинт в сутки
Для цилиндров с уравновешивающим штоком рассчитайте расход смазки отдельно для каждого из двух сальников. В сальниках поршневых штоков для цилиндров высокого давления (>3600 фунтов/кв. дюйм МДРД) используются две точки закачки смазки. Общий расход смазки будет разделен поровну между несколькими точками подачи смазки.
Пример расчета рекомендованного дневного расхода смазки
Компрессор JGJ/2, сжимающий природный газ, соответствующий требованиям к товарному газу (см. рекомендованные значения базового расхода), со следующими значениями фактического диаметра зеркала цилиндра, диаметром поршневого штока 1,5 дюйма (38,1 мм), смазываемый минеральным маслом.
Ряд 1 | Цилиндр J 13,00 дюймов (330 мм), давление нагнетания 100 фунтов/кв. дюйм (6,89 бар). Множитель базового расхода = 1 |
Ряд 2 | Цилиндр J-CE 9,75 дюйма (248 мм), давление нагнетания 577 фунтов/кв. дюйм (39,8 бар), сторона вала. Множитель базового расхода = 1 |
Ряд 3 | Цилиндр J-HE 5,125 дюйма (130 мм), давление нагнетания 1636 фунтов/кв. дюйм (112,8 бар), внешняя сторона. Множитель базового расхода = 1,25 |
Расчет расхода смазки для сальника зеркала цилиндра
Зеркало цилиндра | 13,00 дюймов x 0,4 пинты в сутки на дюйм x 1 = 5,2 пинты в сутки |
Сальник: | 2 x 1,5 дюйма x 0,4 пинт в сутки на дюйм x 1 = 1,2 пинты в сутки |
Зеркало цилиндра | 9,75 дюйма x 0,4 пинты в сутки на дюйм x 1 = 3,9 пинты в сутки |
Сальник: | 2 x 1,5 дюйма x 0,4 пинт в сутки на дюйм x 1 = 1,2 пинты в сутки |
Зеркало цилиндра | 5,125 дюйма x 0,4 пинты в сутки на дюйм x 1,25 = 2,6 пинты в сутки |
Рекомендуемый полный объем, пинт в сутки = 14,1 пинты в сутки |
Примечания.
Рассчитанные выше значения расхода соответствуют «нормальному» расходу смазки при номинальной частоте вращения станины (1800 об/мин).
При работе на более низких скоростях необходимо пропорционально уменьшить расход смазки.
Расход смазки во время приработки будет составлять 150–200% от нормального расхода в течение первых 200 часов эксплуатации.
Приложение B.
Рассмотрение конкретного случая снижения расхода масла на объекте
Оборудование: Ariel JGC/4, 49 000 часов работы
Область применения: сбор газа
Целевое снижение расхода смазки: 50% от номинального расхода смазки
Таблица 2. Условия эксплуатации установки
Ряд | 1 | 2 | 3 | 4 |
---|---|---|---|---|
Ступень сжатия | 3 | Пусто | 2 | 1 |
Давление всасывания, фунтов/кв. дюйм | 450 | НД | 215 | 92 |
Давление нагнетания, фунтов/кв. дюйм | 915 | НД | 460 | 220 |
Об/мин | 1000 об/мин | |||
Относительная плотность | .59 | |||
Область применения | Сбор газа | |||
Нормальный расход смазки | Нечетная сторона — 15 с (22,5 пинты в сутки) Четная сторона — 10 с (26 пинт в сутки) |
|||
Целевой расход смазки (50% от нормального) | Нечетная сторона — 30 с (11,2 пинты в сутки) Четная сторона — 20 с (13 пинт в сутки) |
Резюме для руководства
В целях постоянного совершенствования продукции и сбора данных компания Ariel вместе с одним из своих конечных пользователей работала над снижением расхода смазки, используемой в лубрикаторной системе смазки на одном из их газосборных компрессоров. Целевой расход смазки должен был составлять 50% от нормального расхода смазки, рекомендованного Ariel во время первоначального подбора характеристик компрессора.
Регулярные проверки с заданными интервалами проводились для контроля утечки сальников, диаметров поршневых штоков и качества смазки всех изнашиваемых деталей. Все изнашиваемые компоненты были проверены и измерены для выявления любого ускоренного износа. Не было обнаружено аномального износа, и большинство компонентов по результатам измерений находились в пределах допустимого износа, а некоторые и в пределах производственных допусков Ariel. Интервалы проверок позволили успешно достичь целевого снижения расхода смазки на 50%. Испытание было завершено после окончательной проверки, и установка была снова введена в работу и продолжила работать со сниженным на 50% расходом смазки.
Обсуждение испытаний
Во время капитального ремонта после 50 000 моточасов были установлены новые сальники Ariel со сверхнизким уровнем выбросов (B-7147, B-7109). Кроме того, на этом этапе была проведена проверка цилиндров, поршней, поршневых штоков и сальника, чтобы получить базовое представление о том, как в этих условиях применения работает лубрикаторная система смазки. Проверка показала, что все компоненты, смазываемые лубрикаторной системой смазки, на вид были обильно покрытыми маслом (рис. 2, 3). Основываясь на этом наблюдении чрезмерно смазанной системы, первоначальное сокращение расхода на 10% было пропущено, и расход смазки снизили сразу на 30%.
Спустя 658 часов работы была проведена еще одна проверка для выявления любого аномального износа, утечки сальника, а также для проведения теста папиросной бумагой для определения качества смазывания зеркал цилиндров. На всех этапах проверки утечка сальника отсутствовала. Наружный диаметр каждого поршневого штока измерялся в зоне сальника, чтобы отслеживать любой износ. Поршневые штоки имели состояние новых, и была заметна первоначальная штриховка, нанесенная во время установки. Тесты папиросной бумагой на каждом этапе показывали, что цилиндры все еще смазывались чрезмерно обильно. На основании этой информации расход смазки был снижен еще на 10%, что в общей сложности составило снижение на 40% относительно проектных значений.
Еще через 988 часов установка была снова проверена в соответствии с планом испытаний, который включал проверку утечки сальника, износа поршневого штока и качество смазывания зеркала цилиндра. Все проверки дали исключительные результаты: отсутствие утечек сальника, отсутствие износа поршневого штока и слегка избыточное смазывание зеркал цилиндров. На основе этой проверки уровень смазки был снижен еще на 10%, что в общей сложности составило снижение расхода на 50% относительно проекта.
Еще через 1137 часов (в общей сложности 4655 часов с момента капитального ремонта) установка была снова проверена в соответствии с планом испытаний. Результаты снова были исключительными: отсутствие поддающейся измерению утечки сальника и отсутствие заметного износа на поршневых штоках. На этот раз на зеркалах цилиндров 1-й и 2-й ступеней был обнаружен небольшой избыток смазки, однако тест папиросной бумагой цилиндра 3-й ступени показал, что объем смазки был идеальным. Первый лист папиросной бумаги был полностью пропитан маслом, а второй лист не был пропитан. На этом была достигнута цель снижения расхода смазки на 50%. Дальнейшее снижение расхода смазки не производилось.
Чтобы гарантировать приемлемый срок службы компонентов компрессорной установки, установка была повторно проверена спустя еще 2167 часов (в общей сложности 6822 часа с момента капитального ремонта). Установка продемонстрировала те же характеристики, что и при предыдущей проверке: отсутствие поддающейся измерению утечки сальника, аналогичные результаты теста папиросной бумаги и близкое к новому состояние поршневых штоков. На этом этапе было дождаться отметки в 8000 часов при 50% снижении расхода смазки, чтобы провести окончательную проверку.
По прошествии 8668 часов с момента капитального ремонта и спустя 7022 часа работы со сниженным на 50% расходом смазки установка была демонтирована для проверки на износ зеркал цилиндров, поршневых штоков и поршней, на наличие утечки сальника и качество смазывания всех изнашиваемых компонентов. Поддающиеся измерению утечки сальников отсутствовали.
Износ зеркал цилиндров был в пределах нормы и в большинстве случаев находился в пределах производственных допусков. Поршневые штоки были в близком к новому состоянии и не показали какого-либо износа во время испытаний. Ширина канавок поршневых колец соответствовала возрасту деталей, какие-либо заметные отличия от исходных измерений в начале испытания отсутствовали. Качество смазки на цилиндрах и поршневых штоках было таким же, как и при предыдущих проверках, и был пройден тест папиросной бумагой (рис. 4).
Заключение
Результаты окончательной проверки показали, что снижение расхода смазки на 50% не ускорило износ и не повлияло на утечку сальника. Можно разумно предположить, что аналогичное или по крайней мере значительное снижение может быть достигнуто на сходном оборудовании, которое работает в тех же условиях и с тем же составом газа.