Поршневые компрессоры 21-го века для областей переработки и реализации
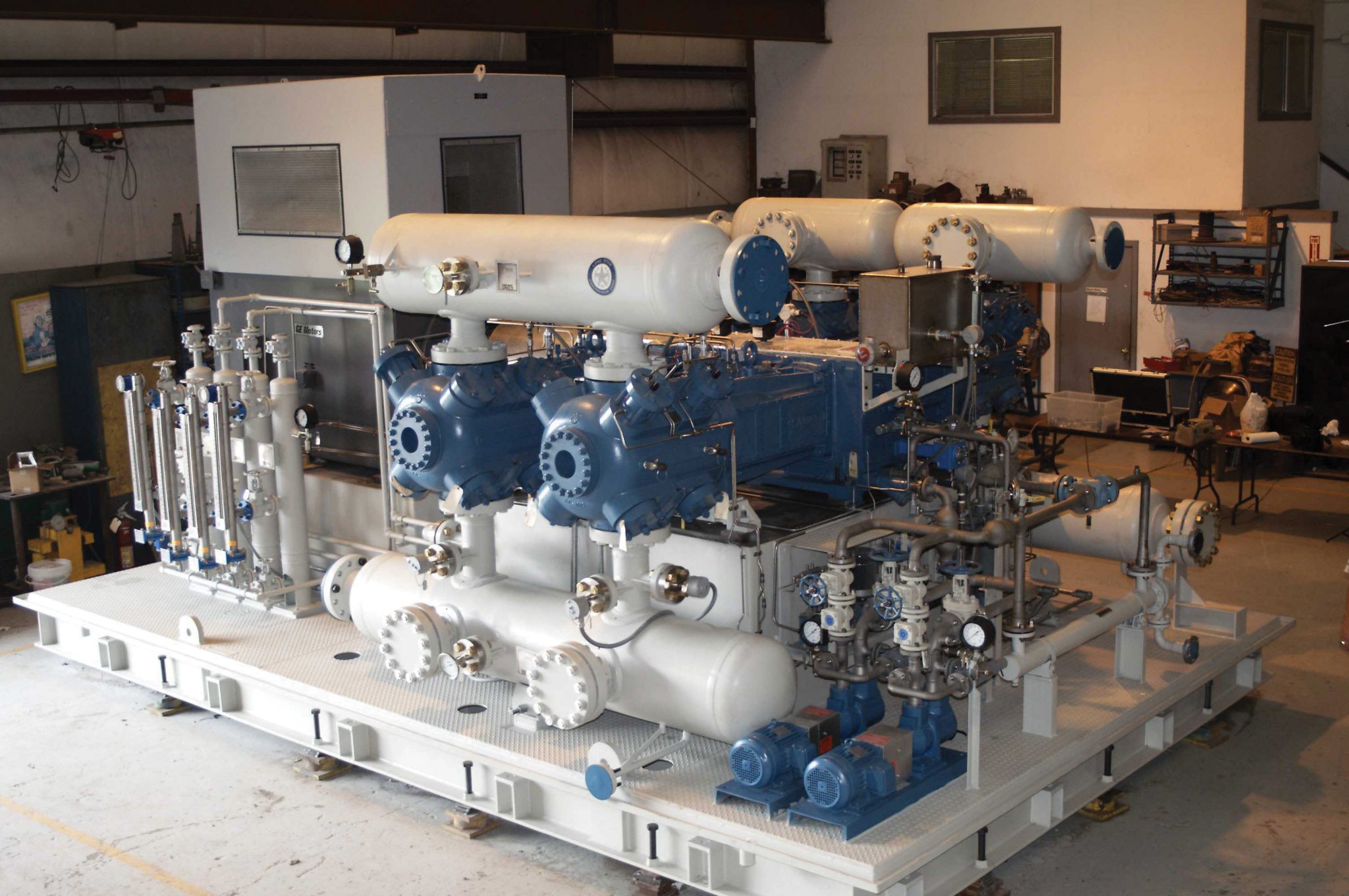
Грег Филлиппи, Ariel Corporation
Опубликовано компанией Hydrocarbon Engineering
Технологии, как и время, не стоят на месте. Подумайте о произошедших за последние 50 лет технологических достижениях. Эти достижения привели нас от перфокарт к медицинским компьютерам, которые можно глотать. На смену дисковым телефонам пришли мобильные. Большинство достижений привели к тому, что средства с тем же функционалом стали меньше и дешевле. Напрашивается вопрос: почему некоторые отраслевые стандарты и люди, которые их пишут, отказываются признать проверенные технологии, которые являются такими же надежными, но менее дорогостоящими, чем те, которые использовались 50 лет назад? В качестве примера рассмотрим отрасль поршневых компрессоров.
В течение почти 100 лет поршневые компрессоры, используемые на этапе переработки и реализации в нефтегазовой промышленности, имели длинный ход и низкую скорость вращения. Начиная с 1964 года, практически все они монтировались на фундаментных блоках, оснащались гильзами компрессорных цилиндров и предусматривали охлаждение согласно стандарту 618 Американского нефтяного института, Reciprocating Compressors for Petroleum, Chemical, and Gas Industry Services (Поршневые компрессоры для нефтяной, химической и газовой промышленности).
Сегодня доступны альтернативные конструкции, предлагающие отрасли аналогичную надежность при более низких капитальных затратах. Некоторые производители предлагают конструкции с более коротким ходом в диапазоне от 76 до 229 мм (от 3 до 9 дюймов) и скоростью вращения от 600 до 1000 об/мин. Эти современные компрессоры устанавливаются в завершенные модули системы компрессии, что способствует снижению капитальных затрат за счет сокращения времени установки и, следовательно, затрат. Многие из этих современных конструкций не используют гильзы и подготовку для охлаждения, как того требует стандарт API 618, что еще больше снижает затраты.
В самых первых поршневых компрессорах использовались технологии паровых двигателей. Такие компрессоры имели ход в диапазоне 914 мм (36 дюймов) или более, а скорость их вращения по сегодняшним меркам была очень низкой — около 100 об/мин. По мере совершенствования технологий производства сальников поршневых штоков и поршневых колец скорость вращения и средняя скорость поршня увеличивались. Например, самый ранний сальник поршневого штока назывался «набивочной коробкой», потому представлял собой цилиндрическую полость, окружающую поршневой шток, в которую вставлялся (набивался) шнур для создания уплотнения. Эта «набивочная коробка» была позаимствована из технологии парового двигателя. Со временем сальники стали значительно более продвинутыми, превратившись в сегментированные наборы колец сальника, изготовленные из различных металлических и неметаллических материалов, столь распространенных сегодня.
Конечные пользователи заинтересованы в повышении скорости вращения и скорости поршня, поскольку повышение обеих величин приводит к снижению капитальных затрат. Повышение скорости вращения и скорости поршня уменьшают физический размер машины, что приводит к уменьшению массы, а значит и стоимости. Сегодня подавляющее большинство поршневых компрессоров, эксплуатируемых на этапе переработки и реализации, приводятся в движение электродвигателями, стоимость которых снижается по мере повышения скорости вращения. Поэтому повышение скорости вращения уменьшает стоимость как компрессора, так и привода.
Сравнение монтируемых на фундаментные блоки компрессоров и модульных компрессоров
Физический размер типового длинноходного (305–508 мм, или 12–20 дюймов) низкоскоростного (250–500 об/мин) компрессора, показанного на рис. 1 и рис. 2, вынуждает монтировать его на объекте (на фундаментные блоки), а не укомплектовывать в готовый модуль на производстве. Большинство поршневых компрессоров, существующих сегодня на нефтеперерабатывающих и нефтехимических заводах, смонтированы на фундаментные блоки. Это означает, что рама компрессора с коленчатым валом строится на заводе, поставляется на место установки, собирается или разбирается (в зависимости от размеров и ограничений на транспортировку), а затем устанавливается на крупный бетонный фундамент («блоки», см. рис. 1). После этого устанавливаются все вспомогательные системы, такие как буферные емкости, сепараторы, технологические трубопроводы, системы смазки, привод, муфта, КИП и система управления. Длинноходные низкоскоростные компрессоры приходится устанавливать таким способом, потому что обычно они очень большие и тяжелые.
Современные среднескоростные короткоходные компрессоры подходят для модульной установки (как показано на рис. 3), поскольку они меньше и легче при той же производительности. Компрессорная установка — это готовый модуль системы сжатия газа, в котором компрессор с приводом, муфтой, технологическим трубопроводом, системами смазки, а также всеми контрольно-измерительными приборами и системами управления смонтирован на стальную раму. Эта рама служит платформой для монтажа всего вышеупомянутого оборудования. Однако во многих случаях она также играет роль фундамента для компрессора.
Сравнение цилиндров с гильзами и без гильз
Стандарт API 618 требует, чтобы компрессорные цилиндры оснащались гильзами. По сути, гильзы используются только по коммерческим причинам. Компрессорному цилиндру не требуется гильза для сжатия газа. Гильзы могут использоваться ввиду следующих причин.
- Гильза может представлять собой более дешевый сменный элемент износа в узле компрессорного цилиндра, тогда как сам сменный корпус цилиндра может быть очень дорогим и иметь длительный срок поставки по сравнению со стоимостью и сроком поставки сменной гильзы.
- Гильза может быть изготовлена из материала, более подходящего для износа, например серого чугуна, тогда как корпус цилиндра изготовлен из материала, неподходящего для износа. Примером такого неподходящего материала является сталь, описываемая стандартом ASTM A395, Standard Specification for Ferritic Ductile Iron Pressure-Retaining Castings for Use at Elevated Temperatures (Стандартные технические условия на отливки из ферритного высокопрочного чугуна, работающие под давлением, для использования их при повышенных температурах). Согласно стандарту API 618 этот материал необходимо использовать для корпусов цилиндров, отлитых из высокопрочного чугуна. Оказывается, что ASTM A395 малопригоден для использования в сферах, где материал подвергается фрикционному износу, как в случае с зеркалом цилиндра, о которое трется поршень и поршневые кольца либо опорные кольца и поршневые кольца. Необходимо уделить внимание защите материала из высокопрочного чугуна A395, и гильза — лишь один из способов добиться этого.
- Использование гильзы позволяет достаточно легко изменять диаметр зеркала цилиндра.
Одной из основных причин отказа от применения гильз в короткоходных цилиндрах является влияние гильзы на рабочий объем цилиндра. Это техническая проблема, которая приводит к значительным коммерческим убыткам. Следующий график на рис. 4 поможет ее объяснить.
Гильза добавляет мертвое пространство фиксированного объема, снижающее рабочий объем. Такое снижение рабочего объема может быть существенным для цилиндров с более коротким ходом. Наличие гильзы также уменьшает объем, который перемещает поршень за полный ход. В сочетании с эффектом от дополнительного мертвого пространства это приводит к значительному уменьшению рабочего объема цилиндра. На графике на рис. 4 учитываются оба эти фактора. Например, рассмотрим диаметр расточки гильзы 300 мм (11,8 дюйма, значение «300» на горизонтальной оси). Фактически это означает, что в цилиндр с диаметром зеркала 325 мм (12,8 дюйма) установлена гильза толщиной 12,5 мм (0,5 дюйма). В итоге рабочий объем цилиндра с зеркалом 325 мм снижен до рабочего объема цилиндра с зеркалом 300 мм. Кроме того, вставка гильзы привела к увеличению объема фиксированного мертвого пространства, что снизило объемный КПД, еще больше уменьшив рабочий объем цилиндра. Для нашего примера диаметра расточки гильзы в 300 мм это снижение рабочего объема составляет порядка 35% для рабочего хода в 76 мм (3 дюйма). Для хода в 457 мм (18 дюймов) снижение составляет 17%, что также значительно. На графике предполагается, что отношение давлений составляет 2,5; а показатель адиабаты газа — 1,4. Предполагаемая толщина гильзы составляет 9,5 мм (0,375 дюйма) для гильз с диаметром расточки до 254 мм (10 дюймов) и 12,5 мм (0,500 дюйма) для гильз с диаметром расточки 254 мм (10 дюймов) и более в соответствии с рекомендациями стандарта API 618.
При заданной требуемой производительности компрессора добавление гильзы требует использования компрессора, который будет больше на процент, показанный на графике. Если снова обратиться к примеру с диаметром 300 мм, компрессор с ходом в 76 мм должен быть больше примерно на 35% для оснащения его цилиндров гильзами. Таким образом, конечному пользователю придется покупать компрессор на 35% крупнее только для того, чтобы установить в цилиндры гильзы.
Кроме гильз, существуют и другие способы защиты высокопрочного чугуна A395 от износа. Другая возможность заключается в упрочнении не оснащенного гильзой зеркала цилиндра для улучшения характеристик износостойкости. Одним из проверенных методов упрочнения является процесс ионного азотирования. Полное описание процесса выходит за рамки данной статьи. Тем не менее, его использование позволяет достичь поверхностной твердости высокопрочного чугуна A395 примерно в 55 единиц по шкале C Роквелла. Этот процесс обеспечивает существенную глубину науглероженного слоя с твердостью около 30 единиц по шкале C Роквелла на глубине 0,15 мм (0,006 дюйма).
Сравнение охлаждаемых и неохлаждаемых цилиндров
Стандарт API 618 также требует, чтобы в компрессорных цилиндрах было предусмотрено охлаждение. На рис. 5 изображен цилиндр с гильзой и охлаждающим кожухом, а на рис. 6 изображен цилиндр без гильзы и без охлаждающего кожуха. Как и гильзы, охлаждение не является необходимым для того, чтобы компрессорный цилиндр сжимал газ.
В стандарте API 618 упоминается один случай, когда может быть полезно предусмотренное конструкцией охлаждение. Там говорится, что это полезно «когда цилиндры эксплуатируются без нагрузки в течение длительного времени». Это относится к ситуации, когда может быть необходимо или выгодно эксплуатировать цилиндр двухстороннего действия, когда внешняя сторона и сторона вала цилиндра одновременно находятся в ненагруженном состоянии. Стандартом требуется использование принудительной жидкостной системы охлаждения, когда может потребоваться эксплуатировать цилиндры в полностью разгруженном режиме. Верно, что в некоторых ситуациях система охлаждения может иметь способность отводить достаточное количество паразитного тепла, образующегося при движении газа в камерах сжатия с внешней стороны и стороны вала, что позволяет «работать полностью без нагрузки в течение продолжительного времени». Не факт, что любой компрессорный цилиндр с принудительным жидкостным охлаждением сможет работать полностью без нагрузки в течение длительного периода времени, поскольку система охлаждения может быть неспособна отводить достаточное количество паразитного тепла, потенциально приводя к преждевременному износу или поломке поршневого кольца, опорного кольца и клапана компрессора.
При обсуждении требований к охлаждению конечные пользователи и производители часто упоминают необходимость использовать охлаждающие кожухи в качестве нагревателей. В этом режиме охлаждающие кожухи используются для нагрева цилиндров перед запуском во избежание конденсации жидкости из газового потока (в результате контакта теплого насыщенного газа с холодным металлом) и повреждения клапанов компрессора или других компонентов при запуске компрессора. Хотя такой способ определенно работает и может быть веским основанием, чтобы использовать цилиндры с охлаждающими (или уже нагревающими?) кожухами, эта проблема возникает не всегда, а избежать конденсации при запуске компрессора можно не только вышеупомянутым способом.
Неохлаждаемые цилиндры успешно используются в отрасли разведки и добычи природного газа на протяжении 50 лет, а в отрасли переработки и реализации — на протяжении 20 лет. Не может быть никаких сомнений в том, что эта технология работает, особенно учитывая, что почти каждый производитель, предлагающий поршневые компрессоры для рынка разведки и добычи и рынка хранения и транспортировки имеет в своей линейке модели с неохлаждаемыми цилиндрами, причем один из таких производителей отгрузил более 150 000 единиц оборудования.
Приведем преимущества технологии неохлаждаемых цилиндров для конечных пользователей.
- Сниженные капитальные затраты, так как нет необходимости приобретения водяной системы кожуха цилиндра.
- Сниженные затраты на эксплуатацию и техническое обслуживание. Отсутствие необходимости эксплуатировать или обслуживать водяную систему кожуха цилиндра.
- Более высокое качество корпусов компрессорных цилиндров. Отливка корпуса неохлаждаемого цилиндра имеет значительно более высокое качество в связи с тем, что ее конструкция не осложнена наличием охлаждающего кожуха. Это также означает более низкую вероятность разрушения конструкции в будущем.
Заключение
Короткоходные среднескоростные поршневые компрессоры, цилиндры которых производятся без использования гильз и охлаждающих кожухов, представляют собой новейшую технологию и являются «поршневыми компрессорами 21-го века для областей переработки и реализации». Эти компрессоры уже занимают доминирующее положение на этапе разведки и добычи и этапе хранения и транспортировки в нефтегазовой промышленности, а также все чаще применяются на этапе переработки и реализации.
Однако многие конечные пользователи отрасли переработки и реализации с неохотой рассматривают короткоходные высокоскоростные компрессоры — в основном из-за опасений относительно надежности. Многим трудно понять, как высокоскоростной поршневой компрессор может иметь надежность, аналогичную низкоскоростному, но это возможно и доказывается каждый день. К примеру, в районе побережья Мексиканского залива в США на установке производства водорода работают два модульных компрессора мощностью 4,1 МВт (5500 л. с.) с длинной хода 146 мм (5,75 дюйма) и скоростью вращения 713 об/мин. Оба компрессора наработали более 24 000 часов бесперебойной эксплуатации, и их капитальный ремонт запланирован на отметке 32 000 часов. Это именно тот успех, который достигается благодаря данной технологии 21-го века. Хотя базовая конструкция поршневого компрессора не сильно изменилась с годами, изменились техники производства, конструктивные возможности, неметаллические материалы и способы моделирования производительности. Современные поршневые компрессоры способны работать при более высоких скоростях вращения и движения поршня без ущерба надежности. Перефразируя рекламу одного производителя автомобилей в США: «Это уже не отцовские поршневые компрессоры».